Coil Coating Process

process different colors for front-
and backside can be applied
The process for coil coating is a highly automated process. There are various coatings performed based on polyester, plastisol, polyurethanes, PVDF, epoxies, primers, backing coats and laminate films. They are applied in a number of layers with various layer thicknesses accordingly to the desired properties of the final steel sheet.
Primer offers two major benefits: it forms the essential link between the pretreatment and the finish coating and it offers a perfect corrosion protection. Primers are a mixture of resin systems. Its characteristics is varying depending on the requirements of the final finish coating. Coil coating has many specific advantages, in particular:
- proven and reliable process (more than 1.3 billion sqm precoated metal is annually used in Europe)
- smooth surfaces with a pure, technical look
- sustainable production (strict process conditions results in high environmental control)
- very good corrosion resistance (pre-treatment and primer offer enormous protection)
- color versatility (any color you like)
- broad range of coatings with specific properties
- reproducibility and flexibility
The coating process happens before end products are fabricated. Coils delivered from the steel rolling mills are placed at the beginning of the coating line. The coils are decoiled led through a strip accumulator to several process units which are:
- cleaning the strip
- power brushing
- surface treatment
- drying
- primer application (one or two sides)
- curing oven and cooling
- coating (one or two sides)
- final cooling down
- rewinding of the coil
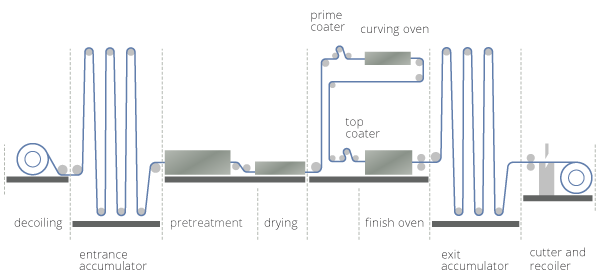
After decoiling the sheet travels throught an accumulator tower into the cleaning section. Both sides of the sheet are washed in a low concentrated alkaline cleaner bath. After brushing and drying the chemical coat is applied followed by infrared ovens. The next step is primer coating - if required - and cured by a dry heat convection oven. The sheet is quenched with cold water and dried again. Now the sheet is well prepared for the finish coating coater, applied on both sides. Before recoiling the sheet is cooled and dried again. If required a protection film will be applied.
Coil coating production lines are pretty fast. The speed is limited by the necessary time drying sheets in the curing ovens. Production line speed about 200 m/min and more can be reached.
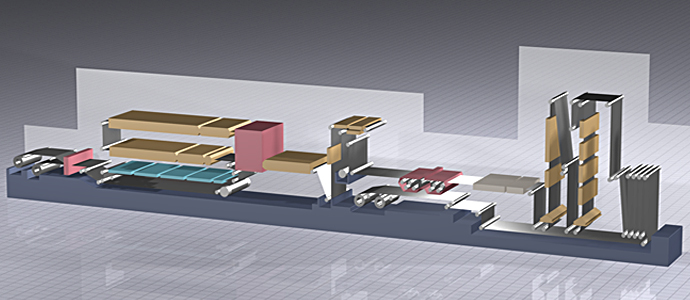
Copyright © 2024 build-your-vision.eu
Coil Coating in Europe
Quote: "Output of the global coil coating industry is around 15 million tons of coated steel, and nearly 1 million tons of coated aluminium per annum. The European industry represents 32% of the production." Source: Heraeus. If divided by different markets the next figur shows the amount of coated steel products used.
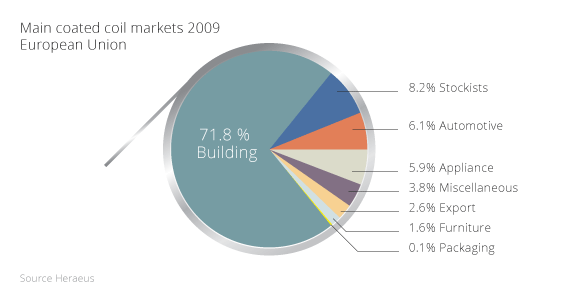